Select a replenishment strategy
by Mayur Vora
Odoo provides two methods for restocking inventory: The reordering rules and the Make to Order (MTO) approach. Although these methods have some differences, they both lead to the automated generation of a purchase or manufacturing order. The decision regarding which method to use relies on the company's manufacturing and delivery procedures.
Terminology
Replenishment report and reordering rules
The replenishment report compiles a list of all products that have an anticipated quantity less than zero.
Reordering rules are implemented to guarantee that a product always has a minimum amount in stock for manufacturing and fulfilling sales orders. When a product's stock level declines to its minimum, Odoo automatically generates a purchase order with the necessary quantity to reach the maximum stock level.
Reordering rules can be established and monitored through the replenishment report or the product form.
Make to Order
The Make to Order (MTO) procurement approach creates a preliminary purchase order or manufacturing order upon the confirmation of a sales order, irrespective of the existing stock levels.
Unlike products restocked using reordering rules, Odoo automatically associates the sales order with the purchase order (PO) or manufacturing order (MO) generated by the MTO method. Another difference between reordering rules and MTO is that Odoo generates a draft PO or MO immediately after the sales order is confirmed with MTO. With reordering rules, Odoo generates a draft PO or MO only when the product's forecasted stock falls below the predetermined minimum quantity. Moreover, Odoo will automatically supplement quantities to the PO/MO as the forecast changes, provided that the PO/MO is not confirmed.
The MTO route is the optimal restocking tactic for personalised products and should only be utilised for that purpose.
Configuration
Replenishment report and reordering rules
To reach the replenishment report, navigate to Inventory ‣ Operations ‣ Replenishment. By default, the report displays all products that necessitate manual reordering. If there isn't any particular rule for a product, Odoo presumes that the Minimum Quantity and Maximum Quantity of the stock are both 0.00.

Note: If there is no established reordering rule for a product, Odoo estimates the forecast by confirming sales orders, deliveries, and receipts. When a product has a set reordering rule, Odoo determines the forecast in a typical way, but also considers the purchase/manufacturing lead time and security lead time.
Ensure that the product has a vendor or a bill of materials configured on the product form before creating a new reordering rule. Furthermore, make sure the Product Type is set to Storable Product on the product form since consumable products do not have their inventory levels tracked, and thus, Odoo cannot account for them in the stock valuation.
To create a new reordering rule from the replenishment report, proceed to Inventory ‣ Operations ‣ Replenishment, press Create, and set the Product. If required, set a Min Quantity and a Max Quantity. Finally, save by clicking Save.
To create a new reordering rule from the product form, go to Inventory ‣ Products ‣ Products, select a product, open its product form, and press the Reordering Rules smart button, followed by Create. Fill in the fields and save the new reordering rule.
By default, the quantity in the To Order field is the amount needed to meet the established Max Quantity. However, the To Order quantity may be adjusted by selecting the field, modifying the value, and saving it. Click Order Once to replenish a product manually.
To automate replenishment, press Automate Orders. When this button is activated, Odoo will automatically generate a draft PO/MO every time the forecasted stock level falls below the set Min Quantity of the reordering rule.
For a given period, a reordering rule may be temporarily deactivated using the Snooze button.
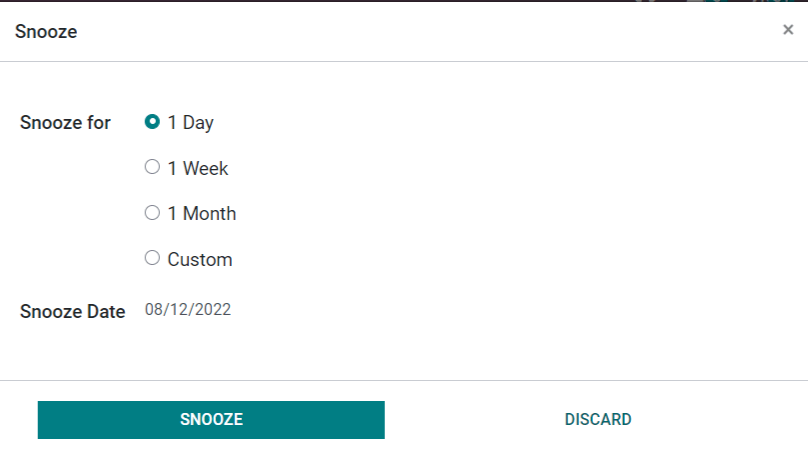
When a purchase order (PO) or manufacturing order (MO) is created through manual replenishment in Odoo, the source document for the order will be listed as the Replenishment Report. However, when a PO/MO is created through an automated reordering rule, the source document will reference the sales order(s) that triggered the rule.
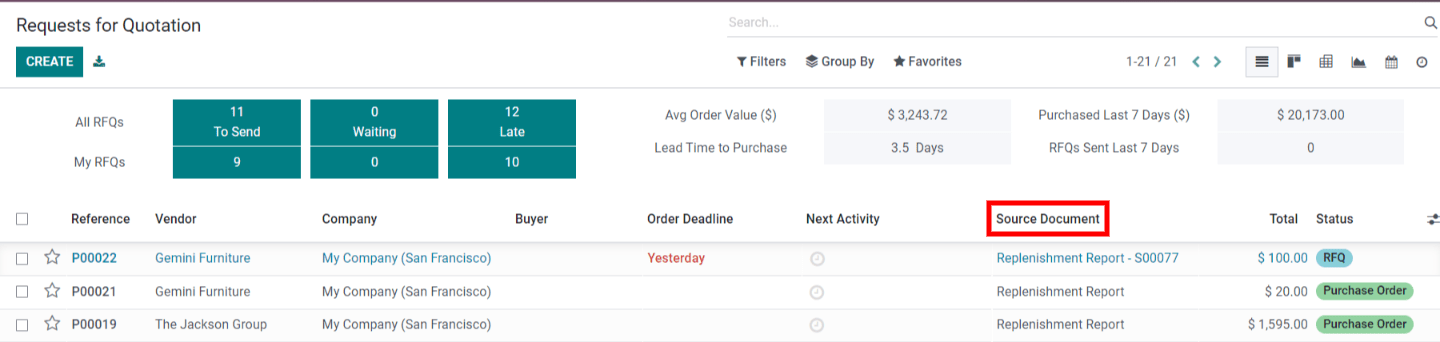
Make to Order
By default, the Make to Order (MTO) route is hidden in Odoo as it is specifically intended for products that require customisation.
To enable the Make to Order (MTO) route in Odoo, follow these steps:
- Go to Inventory ‣ Configuration ‣ Settings ‣ Warehouse.
- Enable the Multi-Step Routes setting and click Save.
- Go to Inventory ‣ Configuration ‣ Routes.
- Click on Filters ‣ Archived to display archived routes.
- Select the checkbox next to Replenish on Order (MTO) and click on Action ‣ Unarchive.
Note: Enabling the Multi-Step Routes setting in the warehouse configuration also enables the Storage Locations setting. If these features are not needed for the warehouse, they can be disabled after unarchiving the MTO route.
To assign the procurement route of a product to MTO, first, go to Inventory ‣ Products ‣ Products, select a product to open its form, and click on the Edit button. Then, switch to the Inventory tab, and under the Routes section, choose Replenish on Order (MTO). If the product is bought directly from a vendor, don't forget to select the Buy route along with the MTO route and set up a vendor in the Purchase tab. For products that are manufactured in-house, select the Manufacture route in addition to the MTO route and configure a bill of materials for the product. Finally, save the changes by clicking on the Save button.
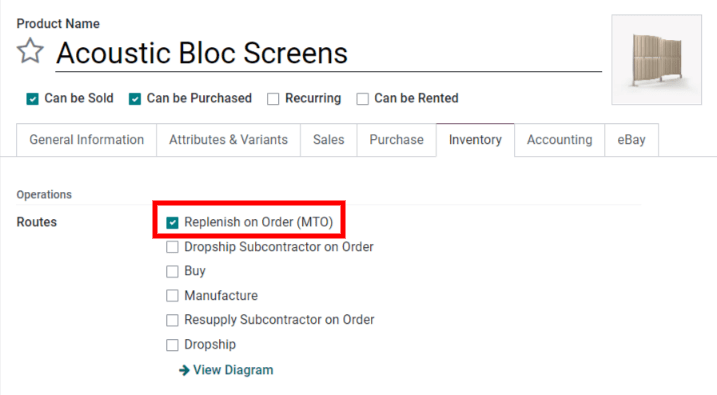